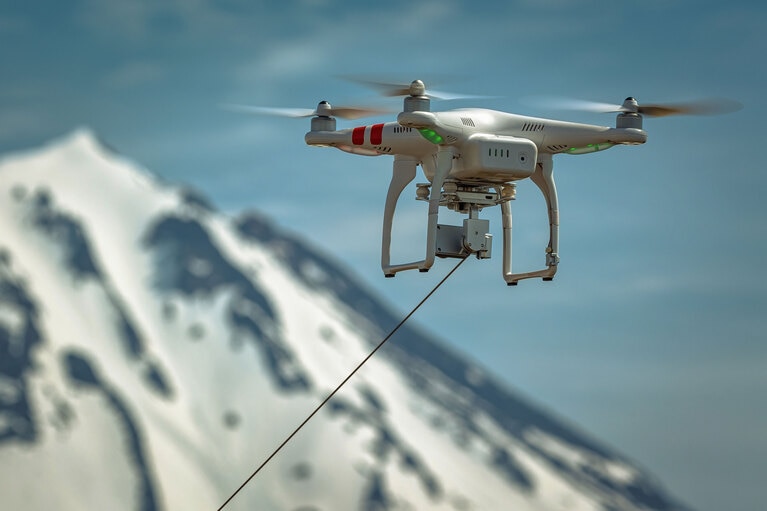
High-density, high-power modules enable lighter, safer, lower cost tether cables to extend missions
This class of unmanned vehicle is powered and controlled via a tether from a ground-based power source assisting in extended missions
Industrial solutions and case studies
Case study: Ultrasonic pipeline inspection
This manufacturer of inspection equipment was looking for ways of improving the integrity of pipeline surveys while reducing the associated downtime. Upgrades to the sensors, cameras and onboard processors, together with the use of higher torque drive motors to provide higher crawler speed, increased the onboard power required. Space and weight for the power supply upgrade was, however, limited. Key goals were:
Onboard the crawler the 24V battery supply was regulated down to 12V for the drive motors, sensors and processor by a DCM DC-DC converter. The small size of the DCM converter, which provided 320W in a package of just 38.7 x 22.8 x 7.2mm, freed up space for the additional sensors.
A DCM converter provided the isolation and regulation for motors and sensors. The rugged packaging and high efficiency (93%) of the DCM converter helped to reduce the operating temperature and improved the reliability of the power solution. To analyze this power chain go to the Vicor Whiteboard online tool.
High-density, high-power modules enable lighter, safer, lower cost tether cables to extend missions
This class of unmanned vehicle is powered and controlled via a tether from a ground-based power source assisting in extended missions
High-efficiency, high-density modules free up space for advanced communications and extend range
High-efficiency class of UAV depend on solar power to meet its long flight time requirements
DCM DC-DC converters double the internal bus power and help keep the aircraft as light as possible
High-altitude long-endurance (HALE) UAVs are essentially flying satellites, designed to operate at extremely high altitudes for extended periods
Lightweight and efficient power modules extend delivery routes and save space to carry more goods
Last-mile consumer delivery of groceries, take-out food and online consumer items is the mission-critical task of autonomous robots