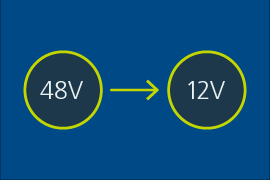
模块化方法解决 48V 电源架构电气化难题
Vicor 功率密度型电源模块是加速汽车电气化的最佳途径。它们灵活、轻便且易于使用,了解更多详情
实现灵活性、可扩展性和最高的功率密度
Vicor 已建立了涵盖产品设计、制造、仿真及选择工具的电源模块能力。这种能力使 Vicor 能帮助电源系统设计人员便捷地部署从电源到负载点 (PoL) 的高性能供电网络 (PDN),以实现扩展至众多不同产业的终端系统,例如汽车、人工智能/数据中心、国防与航空航天以及 LED 照明等。
这种模块化电源组件方法意味着电源行业的一种新标准,可通过一种方法满足现代高性能终端系统不断增长的电源需求,而且能提供更多电源系统优势,例如更少的电源系统空间占用、高效率以及更快的上市进程等。
如今,供电网络在许多行业的大量终端系统中正在迅速发生变化。这些不同系统的电源需求千差万别,因此需要多样化的模块组合,以实现使用模块化电源组件方法的最高灵活性。Vicor 提供的模块化电源解决方案包括:
除了上述这些,还有一些不同的控制特性,例如遥测、补偿和可编程性,以及可能需要的任何行业/安全认证等。
要使用优化的解决方案有效地支持不同行业的不同 PDN,就需要一种全面的电源模块方法。使用电源模块符合大规模定制的实践,而且可获得优势。大规模定制有助于在从通用设计及制造工艺中获益的同时,提供针对不同终端系统优化的独特 PDN。此外,通用可扩展的设计及制造工艺在加速上市进程、可靠性以及技术风险及成本管理方面也具有优势。
Vicor 电源模块方法的关键要素有:
大量电源模块组合可实现多种 PDN 设计,提供了一系列功能、可扩展性及性能。借助电源系统设计工具和白板工具,不仅可从产品系列中为不同的供电架构选择优化的电源模块,而且还可构建最高性能的 PDN(图 1)。这些工具提供了一个环境来分析不同的架构和模块,以针对整体性能、成本或尺寸等考虑因素进行优化。模块化电源组件设计方法是 Vicor 电源模块方法中较为引人瞩目的部分,因为客户每天都会使用它与 Vicor 互动,它由大量的电源模块组合以及用于选择和优化的工具提供支持。电源模块设计本身是 Vicor 电源模块的第二大要素,尽管这对于客户而言并不显眼,但对于提供大规模定制的优势却同样重要。
图 1:使用 Vicor 白板工具设计优化供电网络的示例。
Vicor 对灵活的开关拓扑进行了创新,可适应各种电源转换功能和需求。拓扑的功能各不相同,一个电源模块中可使用一个或多个拓扑。Vicor 正弦振幅转换器 (SAC™) 拓扑是一款最常见的拓扑,可针对不同的电源需求快速配置,主要通过改变模块设计中的 FET 和平面磁性元件实现。使用灵活的开关拓扑,可缩短开发时间,还可以降低为满足特定应用需求而优化的新电源模块的风险。
Vicor 开发了 CM-ChiP™ 通用封装技术,以最大限度提高电源模块的密度和散热性能。CM-ChiP 封装是一种内部有中间层基板的 3D 封装,可将组件布置在上下两面。封装上下两面的热阻抗相等,必要时可进行双面散热。外部电镀选项可为屏蔽和终端连接提供高度的灵活性,包括表面贴装、引脚及底座安装终端。不同的外形或终端连接无需使用工具。使用 CM-ChiP 通用封装技术,可为全新的电源模块设计实现更快的上市进程以及更高水平的性能预测(图 2)。
图 2:与目前同类最佳解决方案相比,Vicor 耐辐射电源模块的功率密度提高了 3 - 5 倍,100V 母线应用的功率损耗降低了 50%。
CM-ChiP 采用面板制造工艺,该工艺与晶圆制造工艺相似。这两种工艺都支持从单块面板或晶圆制造多个模块或器件,可在生产线上实现标准化。该面板可以容纳各种模块外形,并利用整块面板生产尽可多的模块。面板制造工艺是大规模定制的关键要素,可将制造重点从传统的零散化、单一组件封装支持及产量提高转化为涵盖所有产品的面板级工作。
PDN 架构及设计的灵活性包括能够并联大多数电源模块,以充分满足日益增长的系统电源需求。此外,Vicor 还可通过扩大电源模块本身的尺寸来增加模块供电。扩展可通过模块线性扩展来完成,通过将内核模块设计修改为更高的功率水平来提高电源容量。另一个扩展方式是整数扩展,从面板中分离一个以上的基本模块,可实现 2 倍、3 倍,甚至 4 倍的电源容量(图 3)。
图 3:面板制造工艺的缩放方法:线性缩放(左)和整数缩放(右)。
当人工智能 (AI) 处理器电源系统设计人员想在 AI 加速卡上最大限度提高其处理器性能时,他们把目光投向了 Vicor。处理器的电源性能需求要求在 1V 以下的电压下提供 500A 以上的电流。此外,供电网络还需要适应行业标准的开放式计算平台 OAM 卡,突破传统多相降压稳压器的功率密度限制。
图 4:先进的人工智能处理器的供电网络,在低于 1V 的电压下提供 500A 以上的电流。
Vicor 配置了一个基于 SAC™ 拓扑的模块,K 因数为 1/48 的 MCM4609,安装在尺寸为 46 x 9 x 3.2 毫米的 AI 处理器的南北两侧。每个 MCM4609 都能在 1V 以下的电压下为处理器提供总共 325A 或 650A 的稳定电流。MCM4609 从 MCD4609 模块接收驱动信号,形成完整的供电网络。AI PDN提供了无与伦比的密度和接近处理器的位置,最大限度降低了 PCB 损耗。
图 5:用于 AI 处理器供电的 MCM4609 电源模块。
与 AI 处理器的需求类似,在着手开发高密度电动汽车 (EV) 电池 PDN 时,Vicor 能够快速配置一种基于 SAC 拓扑的模块来满足这些需求(图 6)。
图 6:用于 800V 电动汽车电池电源转换的供电网络。
电动汽车除了需要底盘安装封装外,还需要 48V 电源轨,从主电池为汽车中的非电机负载提供支持。要以高效、轻量级的方式从 800V 电池提供 48V 电压,传统解决方案是有局限性的。
因此,Vicor 开发了一种基于 SAC 拓扑的模块, K 因数为 1/16,采用较大的 CM-ChiP 封装(与 AI MCM4609 相比),适应更高的功率以及底盘安装。电源模块 BCM6135 采用 61 x 35 x 7.4 毫米 CM-ChiP 封装,在电流为 80A (或输出功率为 3.8kW)时,可提供 800VIN 至 48VOUT 的转换,效率超过 97%(图 7)。
图 7:用于电动汽车电池电压转换的 BCM6135 电源模块。
BCM6135 下游的其它电源模块支持稳压的 12V 和 48V,形成完整的供电网络。BCM6135 及下游电源模块的高密度和高效率属性可实现更轻的重量以及更高性能的电动汽车电池转换(图 5)。
Vicor 在可配置和可扩展封装方面的创新与电源设计拓扑结构的创新相结合,实现了模块化的 PDN 方法,为众多行业提供了高功率密度和高效率。汽车和数据中心应用解决方案表明,仅仅缩小尺寸是不够的。 最大的影响来自于将这些创新结合起来,并采用模块化方法来解决最棘手的电源挑战。
本文最初由 Power Electronics Europe 发表。